When designing a building, particularly one that will host data centers, office spaces, or any environment that requires extensive cabling and wiring, one of the critical decisions a project manager must make is selecting the appropriate type of access flooring. Access floors are an essential component in modern construction as they provide an easily accessible space for the distribution of electrical, HVAC, and telecommunications services. The two main types of raised access floors are stringerless and stringer access floors. Each has its own set of advantages and applications, and choosing the right one can significantly impact the functionality, flexibility, and long-term maintenance of the facility. This article will delve into the details of stringerless and stringer access floors, helping you make an informed decision for your project.
Understanding Raised Access Floors
Before we compare stringerless and stringer access floors, it’s crucial to understand what access floors are and their purpose. An access floor, also known as a raised floor, is a system that creates an elevated floor above a solid substrate (usually a concrete slab). This elevated floor creates a void for the passage of mechanical and electrical services. Access floors are a common feature in modern offices, data centers, and other environments where there is a need to manage large bundles of cables and provide easy access to those cables for maintenance or reconfiguration.
Components of Raised Floors
Access floors typically consist of the following components:
- Floor Panels: These are the visible surface of the raised floor and are what people walk on. They are usually made of steel, aluminum, or wood and can be covered with a variety of finishes.
- Pedestals: These are the vertical supports that hold the floor panels above the substrate. They can be adjusted to different heights to accommodate varying underfloor space requirements.
- Stringers: In a stringer access floor system, these are the horizontal components that connect the pedestals and provide lateral stability to the floor panels.
- Gaskets: These provide a seal between floor panels to prevent airflow and the passage of particles between the underfloor and the occupied space.
Stringerless Raised Access Floors
Stringerless access floors rely solely on the strength of the pedestal and the floor panel design to maintain stability. They do not use horizontal stringers to connect the pedestals. This design offers a few distinct advantages:
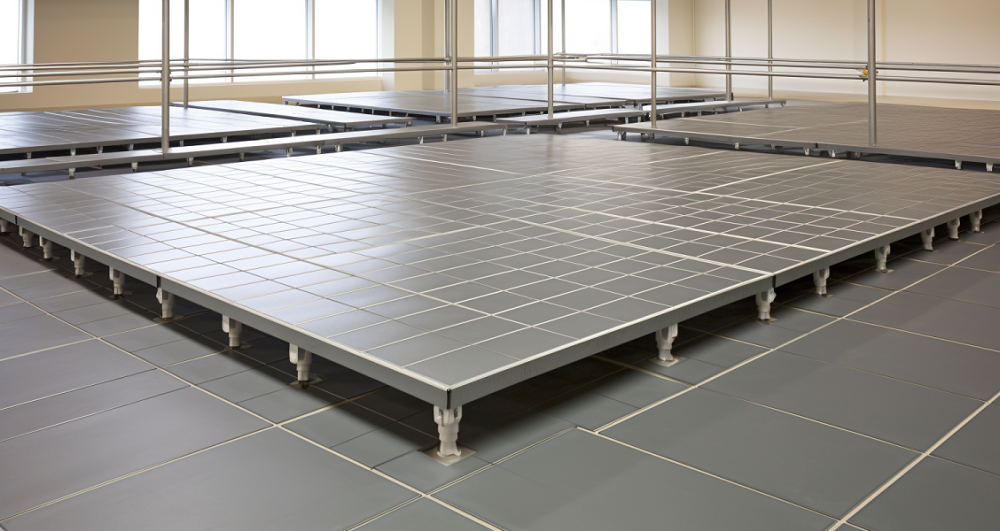
Pros:
- Flexibility: Without stringers, the underfloor space is more accessible, allowing for easier reconfiguration of services as necessary.
- Cost: Stringerless systems are typically less expensive than stringer systems because they have fewer components.
- Installation: They are generally quicker and easier to install, as there are fewer parts to assemble.
Cons:
- Stability: Stringerless floors may not provide the same level of lateral stability as stringer systems, especially over large spans.
- Load Capacity: They may have lower load capacities, making them less suitable for environments with heavy equipment.
Stringer Raised Access Floors
Stringer raised floors incorporate stringers, which are horizontal bars that connect pedestals to add stability to the raised floor system. This design is prevalent in applications where a higher degree of stability and load capacity is required.

Pros:
- Stability and Load Capacity: The inclusion of stringers makes these systems more stable and capable of supporting heavier loads.
- Performance: Stringer systems often have better performance in terms of acoustics and vibration reduction.
- Alignment: Stringers help maintain the alignment of floor panels, which can be especially important in areas with high traffic or heavy equipment.
Cons:
- Cost: They are generally more expensive than stringerless systems due to the additional materials and complexity.
- Installation: Installation can be more time-consuming and complex.
- Flexibility: The presence of stringers can make it more difficult to access the space beneath the floor for maintenance or reconfiguration.
Differences Between Stringer Raised Floor and Stringerless Raised Floor
Below is a comparison table that outlines the main differences between StringerlessAccess Floor and Stringer Access Floors:
Feature | Stringerless Access Floors | Stringer Access Floors |
Stability | Moderate stability | High stability |
Load Capacity | Lower load capacity | Higher load capacity |
Flexibility | More flexibility for reconfiguration | Less flexibility; more fixed |
Installation Complexity | Less complex, quicker installation | More complex, longer installation |
Cost | Typically lower cost | Higher cost |
Underfloor Accessibility | Easier access to underfloor space | Restricted access due to stringers |
Alignment | Risk of misalignment | Consistent alignment |
Acoustics and Vibration | May not perform as well | Better performance |
Sealing and Contamination Control | Less effective sealing | Better sealing capabilities |
Aesthetics | Similar aesthetic options | Similar aesthetic options |
Adaptability to Change | Highly adaptable | Less adaptable |
Building Code Compliance | Must comply with codes, may have limitations | Must comply with codes, sometimes required |
Application | Office spaces, computer rooms, and areas where the load is moderate and flexibility is required | Data centers, server rooms, and areas with heavy equipment or need for stringent contamination control |
When selecting an access floor system, it’s essential to consider the specific needs and requirements of your project, including the intended use of the space, the expected traffic, the types of equipment to be supported, and the need for future flexibility. Always consult with a structural engineer or a specialist in access flooring to ensure that your choice meets all technical and safety standards.
Stringer Raised Floor vs Stringerless Raised Floor: Which One To Choose?
When choosing between stringerless and stringer access floors for your project, several factors should be considered:
- Budget: Determine the project’s budget for the raised floor system, as this may limit the options.
- Load Requirements: Assess the expected load requirements of the space. For areas that will support heavy equipment, a stringer system may be necessary.
- Flexibility: Consider how often the underfloor services will need to be accessed and reconfigured. If frequent changes are anticipated, a stringerless system may offer more convenience.
- Building Code Requirements: Check local building codes and regulations, as they may influence the type of system you can use.
- Future Needs: Think about the potential for future changes or expansions to the building’s services and how each type of system can accommodate those needs.
- Environmental Control: If your space requires strict control over air flow or contamination, the seal provided by a stringer system might bemore beneficial.
- Professional Consultation: It is wise to consult with an architect or engineer who has experience with raised floor systems to understand the implications of each type for your specific application.
- Vendor Options: Investigate different manufacturers and vendors, as they may offer variations on stringer and stringerless systems that could influence your decision.
- Maintenance Considerations: Think about the maintenance demands of your facility. If you require easy and frequent access to the area beneath the floor, a stringerless system could be more practical.
- Aesthetics: While functionality is paramount, consider the finished look of each type of system, especially if the space will be client-facing or used for presentations.
Case Studies and Real-World Applications
To help illustrate the decision-making process, let’s look at a couple of case studies:
Case Study 1: Data Center
A high-tech data center requires a robust access floor system to support the weight of servers and cooling units. The facility also needs to ensure excellent air distribution and control for cooling purposes. In this scenario, a stringer access floor system might be the preferred choice due to its higher load capacity and the ability to provide a sealed environment that can effectively manage airflow.
Case Study 2: Office Renovation
An office space is being renovated with the intention of creating a modern, flexible work environment. The design calls for an access floor system that can be quickly reconfigured as teams change and technology evolves. A stringerless access floor system may be selected here for its flexibility, ease of access, and lower cost.
Choosing between a stringerless and a stringer access floor system depends on a multitude of factors related to the specific needs of your project. While stringer systems offer greater stability and load-bearing capacity, stringerless systems provide superior flexibility and are often more cost-effective. It’s essential to thoroughly evaluate all aspects of your project, including budgetary constraints, load requirements, and the need for flexibility, before making a decision.
Ultimately, the right choice will provide a solid foundation for the infrastructure of your building, supporting not just the physical weight of your equipment but also the dynamic needs of technology and people who use the space. As with any significant construction decision, consult with industry professionals and use the information provided here as a guide to inform your selection process for an access floor system that will serve your project well into the future.