ISO Class 7 cleanrooms provide stringent contamination control while balancing practical operational requirements, as classified by the ISO. These controlled environments meet standards for low particulate counts and carefully regulated parameters for humidity, gowning, and temperature. ISO 14644 standards govern cleanroom classifications, with ISO Class 7 having specific defined requirements compared to more restrictive ISO Class 5 cleanrooms. Understanding ISO Class 7 cleanrooms is important for industries like pharmaceuticals, biotech, and electronics manufacturing to maintain compliance and optimal product quality within critical environments where contamination can significantly impact manufacturing processes.
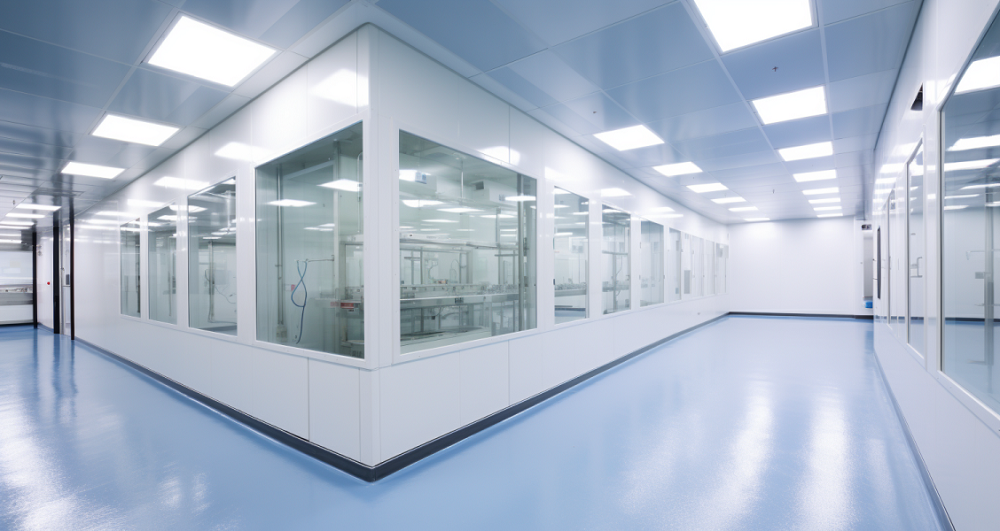
What is ISO Class 7 Cleanroom?
An ISO Class 7 clean room is defined by the International Organization for Standardization (ISO) and is classified by the number and size of particles permitted per volume of air. This classification is part of the ISO 14644-1 standard, which is the primary, worldwide standard for cleanroom classification and testing.
ISO Class 7 Cleanroom Particle Counts
How many particles are in a ISO class 7 cleanroom? For an ISO Class 7 cleanroom, the following are the maximum allowable particle counts:
- Not more than 352,000 particles per cubic meter of a size 0.5 µm or larger
- Not more than 83,200 particles per cubic meter of a size 1.0 µm or larger
- Not more than 29,300 particles per cubic meter of a size 5.0 µm or larger
Here is a table comparing the maximum particle counts for different particle sizes within an ISO Class 7 cleanroom:
Particle Size (micrometers) | Maximum Particles/m³ |
0.1 | Not defined |
0.2 | Not defined |
0.3 | 1,020,000 |
0.5 | 352,000 |
1 | 83,200 |
5 | 2,930 |
To maintain this level of cleanliness, ISO Class 7 cleanrooms use High Efficiency Particulate Air (HEPA) filters to capture particles, as well as strict protocols for clothing, equipment, and cleaning procedures. These cleanrooms are used in various industries where small particles can adversely affect the manufacturing process, such as pharmaceuticals, biotech, and electronics manufacturing.
ISO Class 7 Cleanroom Standards
The standard for ISO Class 7 cleanrooms is ISO 14644. This standard provides specifications for cleanroom classification based on the concentration of airborne particles. ISO 14644 consists of multiple parts, and for cleanroom standards, the following parts are particularly relevant:
- ISO 14644-1: Classification of air cleanliness by particle concentration. This part of the standard specifies the classification of air cleanliness in terms of concentration of airborne particles in cleanrooms and clean zones.
- ISO 14644-2: Monitoring to provide evidence of cleanroom performance related to air cleanliness by particle concentration. This part of the standard specifies minimum requirements for periodic testing of a cleanroom or clean zone to prove its continued compliance with ISO 14644-1.
- ISO 14644-4: Design, construction, and start-up. This part of the standard specifies the requirements for the design and construction of cleanroom facilities.
- ISO 14644-5: Operations. This part of the standard specifies the requirements for the monitoring of cleanroom and clean zone performance related to air cleanliness by particle concentration.
These standards provide detailed guidelines for the design, construction, operation, and monitoring of cleanrooms in various industries. They cover aspects such as cleanroom classification, monitoring procedures, design and construction requirements, and operational considerations. It’s important to note that standards are periodically updated, so it’s essential to refer to the latest version of ISO 14644 or any other relevant standards to ensure compliance with current requirements for ISO Class 7 cleanrooms.
ISO Class 7 Cleanroom Requirements
ISO Class 7 cleanrooms must meet specific requirements to achieve the necessary environmental cleanliness level. Here are some of the key requirements based on the ISO 14644-1 standards:
- Air Quality: ISO Class 7 cleanrooms require a maximum allowable concentration of particles per cubic meter. For ISO Class 7, this limit is 352,000 particles ≥ 0.5 microns in size per cubic meter of air.
- Airflow: The airflow in a cleanroom is designed to ensure that particles are carried away from the critical area. Proper circulation and filtration systems are essential to maintain the cleanliness of the air.
- Air Change Rate: The air change rate refers to how many times the air within a cleanroom is replaced per hour. For an ISO Class 7 cleanroom, the air change rate should be carefully controlled and typically falls within a specific range to maintain the required cleanliness.
- Temperature and Humidity Control: Cleanrooms often require strict control over temperature and humidity to ensure that the environment remains stable and suitable for the processes being conducted within them.
- Cleanroom Design and Materials: The design and construction materials of a cleanroom are crucial to maintaining the desired air quality. Walls, ceilings, floors, and all surfaces must be easy to clean and resistant to particle generation.
- Personnel Protocol: People are a significant source of particulate contamination. Personnel entering ISO Class 7 cleanrooms are usually required to wear specific cleanroom garments, such as coveralls, hoods, gloves, and booties, as well as to follow strict protocols for entering and exiting the cleanroom environment.
- Equipment and Tooling: All equipment, tools, and materials brought into the cleanroom must be carefully selected, and in many cases specially designed, to minimize particle generation and contamination.
- Monitoring and Validation: Continuous monitoring is essential to ensure that a cleanroom maintains its required level of cleanliness. This includes particle counters, air pressure differentials, temperature, and humidity monitoring.
It’s important to note that specific requirements might vary depending on the industry and the particular processes being performed in the cleanroom. Organizations should refer to the most current version of ISO 14644-1 and any other relevant standards or regulations applicable to their operations for comprehensive requirements.
While ISO 14644-1 provides the classification of cleanrooms based on particulate concentration, the specific requirements for humidity, gowning, and temperature can vary depending on the application of the cleanroom. Here are some typical requirements for these parameters in an ISO Class 7 cleanroom:
ISO Class 7 Cleanroom Humidity Requirements
Humidity levels are usually set to minimize the risk of electrostatic discharge (ESD), which can be a significant concern in electronic manufacturing, or to prevent product spoilage or degradation in pharmaceutical and biotech applications.
Typical relative humidity (RH) levels for an ISO Class 7 cleanroom might range from 45% to 55%, but this can vary. For example, some processes may require lower humidity levels (as low as 30% RH), while others might need higher levels.
Humidity control must be precise, often with tight tolerances, to ensure process stability and product quality.
ISO Class 7 Cleanroom Gowning Requirements
Personnel working in an ISO Class 7 cleanroom typically wear full-body garments, head coverings, face masks, gloves, and shoe covers or dedicated footwear. The exact requirements can depend on the processes being performed.
The gowning process often involves multiple steps to prevent contamination from being brought into the cleanroom. These steps are usually performed in a gowning room or airlock to create a buffer zone between the cleanroom and non-controlled environments.
Gowning procedures may also include the use of tacky mats to remove particles from shoe soles, hand washing or sanitizing, and the proper donning of cleanroom garments in a specific sequence to minimize contamination.
ISO Class 7 Cleanroom Temperature Requirements
The temperature in an ISO Class 7 cleanroom is typically set for the comfort of the personnel and to maintain the integrity of the process and products. This might be in the range of 20°C to 22°C (68°F to 72°F), but again, this can vary widely depending on the specific processes and equipment used in the cleanroom.
Temperature control must be consistent, as fluctuations can affect both the cleanroom’s air pressure and the behavior of particles, as well as potentially impacting the processes being carried out within the cleanroom.
In addition to these general guidelines, each facility may have its own set of more stringent requirements based on the type of work being done in the cleanroom. It’s crucial for organizations to consult with process engineers, quality control specialists, and compliance officers to ensure that their cleanroom environment meets all necessary operational and regulatory standards.
Differences Between ISO Class 5 Cleanroon vs. ISO Class 5 Cleanroon
Here are some key differences between ISO Class 7 and ISO Class 5 cleanrooms:
Characteristic | ISO Class 7 Cleanroom | ISO Class 5 Cleanroom |
Particle contamination level | ≤10,000 particles/m3 of ≥0.5 μm | ≤35,200 particles/m3 of ≥0.5 μm |
Airflow | Lower air change rate; less stringent airflow control | Higher air change rate; more stringent airflow control |
Air changes per hour (ACH) | Minimum 120 ACH | Minimum 120 ACH |
Pressure differential | Slight positive pressure in cleanroom relative to surrounding areas | Slight positive pressure in cleanroom relative to surrounding areas |
Air filters | HEPA and ULPA filters used | HEPA and ULPA filters used |
Garbing requirements | Minimal garbing such as lab coats and shoe covers | Full gowning including hair covering, face masks, gloves |
Surface contamination controls | Guidelines for surface particle and microbial limits | Stricter guidelines for surface particle and microbial limits |
Temperature requirements | Slightly less precise temperature control | More precise temperature control |
Humidity requirements | Slightly less stringent humidity control | More stringent humidity control |
Cleanroom Design | Design may be less stringent; materials may be less specialized | Typically more robust construction materials and design features |
Maintenance requirements | Regular filter changes and cleaning | More frequent filter changes, cleaning, and stringent monitoring |
Personnel Protocol | Gowning and entry/exit protocols are less stringent | More stringent gowning and entry/exit protocols |
Equipment Requirements | Requirements for equipment are less stringent | More stringent requirements for equipment to minimize particle generation |
Monitoring frequency | Regular particle sampling | Continuous particle monitoring |
Industry Applications | Used in applications such as some pharmaceutical processes, some biotechnology processes, and certain types of research and development | Typically used in more critical applications such as semiconductor manufacturing, pharmaceutical production, and nanotechnology |
Cost to build and maintain | Lower costs than ISO Class 5 | Higher costs due to stringent requirements |
ISO Class 7 cleanrooms have higher particulate contamination limits than Class 5, requiring less stringent garbing, surface controls, monitoring and maintenance which makes them more affordable to build and operate compared to ISO Class 5 cleanrooms.
If you are creating your ISO Class 7 Cleanroon and want to find the best flooring solution for it, our cleanroom raised floor system can be the best choice. If you are interested, please get in touch with our experts!