Raised flooring is an advanced flooring system with many advantages and areas of application. However, due to its special structure and installation method, the raised floor requires effective moisture-proof measures. This article will discuss why raised floors need to be moisture-proof and how to prevent moisture, aiming to help readers better understand and apply raised floor systems.
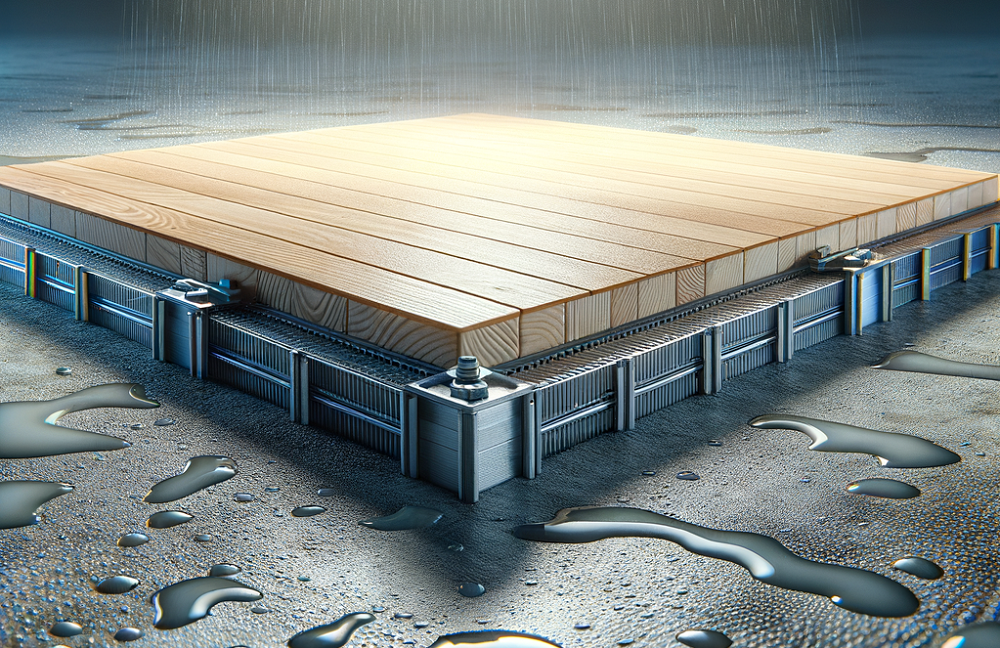
Why Should Raised Floors Be Moisture-Proof?
To fully understand the importance of moisture-proofing raised floors, let’s first provide an overview of raised floor systems. Raised floor systems are an innovative flooring solution that offers many advantages in applications such as office buildings, commercial premises, industrial plants and sports venues by spatializing the floor above. However, due to the special construction of a raised floor, it is more susceptible to moisture and moisture.
The dangers of moisture and moisture to floors cannot be ignored. They can penetrate into the space beneath the floor, causing problems such as swelling, deformation, decay, and mold growth in the flooring material. Not only does this affect the appearance and performance of the floor, it can also have a negative impact on the indoor environment and the health of users. Therefore, raised floors must take moisture-proof measures for the following reasons:
1. Prevent mold and deformation of floors
If it is in a humid environment for a long time, the cavity floor will easily accumulate moisture, and problems such as mildew and warping will occur inside the floor. In severe cases, it may cause the floor to crack, break, and fall off, which not only affects use, but may also cause safety hazards. Taking moisture-proof measures can avoid moisture absorption and deformation of the floor and ensure the quality of the floor.
2. Prevent steel structure from rusting
The main load-bearing structures of the elevated floor are steel beams, steel plates, etc. These steel structures are prone to rust once exposed to water. The corrosion inside the floor not only affects the load-bearing capacity of the floor, but may also cause the floor to crack and collapse. Therefore, moisture-proof measures must be taken to avoid corrosion of the steel structure and ensure the safety of the floor.
3. Reduce disease infection and odor
Damp floors can easily accumulate mold, bacteria, etc., which can be harmful to human health and may cause respiratory diseases or allergic reactions. At the same time, wet floors can also produce an unpleasant musty smell. Moisture-proofing can reduce the growth of germs and odors and ensure the hygienic conditions of the floor.
4 .Prevent pipeline and electrical failures
Water supply and drainage pipelines, wires, etc. are often arranged in the raised floor space. Once these pipelines and electrical equipment encounter water, they are prone to leaks, short circuits, fires and other failures. Taking moisture-proof measures can reduce the erosion and damage caused by moisture to pipelines and electrical appliances, ensuring the normal operation of the floor system.
5. Save on repair costs
Moisture-proof flooring lasts longer and can reduce the cost of frequent repairs and updates caused by water damage. Failure to protect against moisture will lead to frequent problems with the floor, which can be very costly to repair. Taking moisture-proof measures can save later repair expenses.
Raised floors are very susceptible to moisture attack. Moisture-proof measures must be taken to ensure the performance and safety of the floor, avoid moisture damage to the floor, extend the service life, save maintenance costs, and ensure long-term normal use of the floor.
How To Protect Raised Floors from Moisture?
In order to effectively prevent moisture and water from invading the raised floor system, moisture-proof treatment can be carried out from the following aspects during the design, construction, and use process:
1. Strengthen ground waterproof layer
A waterproof layer, such as a two-component waterproof coating, can be painted on the ground under the elevated floor to form a waterproof film on the ground to block the penetration and rise of groundwater into the floor. You can also lay waterproof membranes on the ground to enhance the anti-seepage performance of the ground.
2. Installation of moisture-proof isolation layer
Before installing a raised floor, a moisture barrier should be added to the floor base. The moisture-proof isolation layer is usually made of materials such as plastic film or waterproof membranes. When installing, it must ensure that it completely covers the ground, and there must be overlap and sealing between each part to ensure the moisture-proof effect.
3. Floor perimeter waterproof mat
A waterproof pad is installed around the elevated floor at the connection between the wall and the floor. It is made of waterproof material and can prevent water from seeping through the wall into the cavity at the bottom of the floor. Commonly used waterproof pad materials include rubber, PVC, EPDM, etc.
4. Tips for seam sealing
There are seams between the modules of the raised floor that need to be sealed. Seams can be filled with waterproof glue or sealant to ensure they are waterproof. When sealing, pay attention to cleaning the seams to ensure good adhesion and tightness.
5. Reinforce floor bottom
Use waterproof steel plates to reinforce the bottom of the elevated floor to prevent direct contact with moisture. The bottom of the steel plate is painted with anti-rust paint to enhance its anti-corrosion properties. Polyurethane waterproof coating can also be sprayed on the bottom to form a waterproof film.
6. Install floor drain
Set up a floor drain at an appropriate location around the floor and connect it to the drainage pipe inside the floor. When there is water leakage inside the floor, it can be drained in time to avoid water accumulation. The number and location of floor drains should be reasonably designed based on the floor area.
7. Improve the anti-corrosion level of supporting structures
The floor steel support structure should use materials with higher anti-rust specifications and undergo anti-rust treatment to improve corrosion resistance. Connectors should also be made of anti-corrosive materials or treated with anti-corrosion treatments.
8. Install floor ventilation system
Set ventilation holes at appropriate locations inside the elevated floor and connect them to ventilation ducts. Use ventilation equipment to ventilate the space inside the floor, reduce the humidity inside the cavity, and prevent water accumulation.
9. Choose moisture-proof floor materials
In a raised floor system, it is crucial to choose materials with excellent waterproofing properties. For example, polymer composites and rubber have excellent water-repellent properties and can effectively resist moisture penetration. When selecting materials, also consider their durability, and resistance to mildew and corrosion.
10. Properly set the floor water slope
The floor must have a certain water slope so that water on the floor surface can quickly flow to the drainage system and prevent water from accumulating on the floor. The water crossing slope is generally 1%-2%.
11. Practical recommendations for installation and maintenance
When installing a raised floor, follow the manufacturer’s instructions and ensure the correct installation and tight connection of individual components. Carry out regular floor maintenance and upkeep, including cleaning, checking the status of joints and drainage systems, and promptly repairing and replacing damaged parts to ensure that the moisture-proof effect is long-lasting and effective.
Raised Access Floor Moisture-Proof Success Cases
- Moisture-proofing practices for raised floors in commercial buildings
In commercial buildings, raised floors are widely used in office buildings, shopping malls, hotels and other places. By using waterproof materials, moisture-proof isolation layers and reasonable drainage systems, moisture and moisture can be effectively prevented from invading the floor and the stability and beauty of the floor can be protected. - Raised floor moisture-proof case in industrial environment
Industrial plants often face moisture and humidity challenges, and raised floor systems offer advantages in this environment. By selecting materials with strong water resistance, strengthening the installation of moisture-proof isolation layers and properly designing drainage systems, you can ensure long-term stable operation of floor systems in industrial environments.
Through the comprehensive adoption of the above moisture-proof measures, the raised floor can be effectively protected from moisture and its service life can be extended. Moisture-proof work must run through the entire process of floor design, construction, and use, and multiple moisture-proof measures must be taken to ensure long-term normal use of the floor.